What is a palletizing robot? What is the principle of a palletizing robot?
Date:2021-01-13
A Palletizing robot (Techrobots) is a mechanical device used to perform work automatically. In use, it can be commanded by humans, and can run pre-arranged programs correctly, and can act according to principles and guidelines formulated with artificial intelligence technology. , Put the objects in the container on pallets and pallets (wood, plastic) according to a certain arrangement, and stack them automatically. It can be stacked in multiple layers and then pushed out to facilitate forklifts to transport to the warehouse for storage. Its purpose is to assist or replace human repetitive work, such as the production industry, the construction industry can be applied.
Palletizing robots (Techrobots) can be integrated into any production line to provide intelligence, robotics, and networking for the production site. It can realize palletizing logistics for a variety of operations in the beer, beverage, and food industries. It is widely used in a carton, Plastic boxes, bottles, bags, barrels, film packaging products and filling products, etc. It is matched with the three-in-one filling line, etc., to palletize various bottles, cans, and bags. The automatic operation of the palletizer is divided into automatic loading, turning, sorting, stacking, shifting, lifting, loading, unloading, and unloading steps.
Palletizing robot gripper principle
Palletizing robots (Techrobots) mostly perform pick-and-place operations, that is, the robot grabs materials from the conveyor belt and places them on the pallet at the specified position along the motion path. Therefore, according to the positional relationship between the robot and the conveyor belt and the pallet when the robot completes the palletizing operation, comprehensively considering the obstacles in the movement process, the "door"-shaped movement track is selected. Note that when the robot end-effector completes the stacking of cartons at different positions on the pallet, the trajectory is all in the shape of a "door", and only the coordinates of the trajectory endpoint are different due to the different positions of the cartons on the pallet.
The so-called palletizing is based on the idea of integrated unitization, stacking materials according to a certain pattern into a stack, so that the unitized material stack can realize the storage, handling, loading and unloading, transportation, and other logistics activities of materials. Compared with traditional manual palletizing and gantry palletizers, palletizing robots have gradually been applied to various fields due to their high production efficiency, small footprint, large movement flexibility, and low labor intensity.
Commonly used palletizing robot hand grip
· Gripper type manipulator claw: mainly used for high-speed code bags;
· Splint type manipulator claw: mainly suitable for box stacking;
· Vacuum suction manipulator claw: mainly suitable for suckable stacking objects;
· Hybrid gripping manipulator claw: mainly suitable for picking up and stacking objects;
· Hybrid gripping manipulator claw: suitable for collaborative gripping and placing of several stations.
When using a palletizing robot, one important thing to consider is how the robot grasps a product. The vacuum gripper is the most common end-of-arm tool (EOAT). Relatively speaking, they are cheap, easy to operate, and can efficiently load most loads. However, in some specific applications, vacuum grippers may also encounter problems, such as porous substrates, flexible packaging with liquid content, or packaging with uneven surfaces.
Palletizing robot classification
1. According to the structure
According to the different mechanical structures, the palletizing robot includes the following three forms: Cartesian, rotary joint, and gantry crane.
① Cartesian palletizing robot: mainly composed of four parts: upright column, X-direction arm, Y-direction arm, and gripper, complete the palletizing of materials with four degrees of freedom (including three moving joints and one rotating joint). This type of palletizer has a simple structure, strong body rigidity, and large carrying weight, which is suitable for palletizing heavier materials.
② Rotary joint robot: The palletizer rotates around the body and includes four rotary joints: waist joint, shoulder joint, elbow joint, and wrist joint. This form of palletizer is programmed by teaching, that is, the operator holds the teaching box and controls the robot to move according to the prescribed action, so the moving process is stored in the memory, and this can be reproduced during automatic operation later. One exercise process. This kind of robot has a small body and a large range of motion. It can palletize one or several pallets at the same time, and can flexibly and flexibly work on a variety of product production lines.
③Gantry crane type: The robot arm is installed on the gantry crane as a gantry type palletizing robot. This type of palletizing robot has a large working range and can grasp heavier materials.
2. Divided according to stacking requirements
①Single layer palletizing robot
The single-layer palletizing robot is relatively basic. It mainly relies on the conveyor belt to transport materials. When it reaches the steering mechanism, it can be adjusted according to the specified direction. After preparation, it can enter the layer conveying mechanism. As long as the products are arranged tightly in this place according to the set arrangement order, the arranged products are transferred to the next station through the conveyor roller, so that the stacking operation of the palletizing robot is completed.
②Multilayer palletizing robot
There must be multiple layers corresponding to a single layer, which is definitely more complicated than a single layer palletizing robot. We can see whether the carrier board of the multi-layer palletizing robot is under the conveyor belt, or it can be left and right. When the machine is stacking, the materials will be neatly arranged on the pallet, and then the pallet will be set at the left limit position. When the materials conveyed by the conveyor belt are blocked by the baffle, they are arranged in a row. Then the pallet is moved to the right, and the materials will be lined up again like the steps above. By analogy, for each additional layer of material, the height of the lifting platform of the palletizing robot will drop by one layer until the material is stacked to a certain height and then stop.
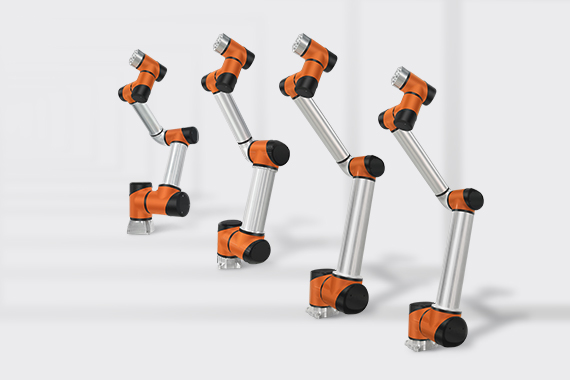
Palletizing robot gripper principle
Palletizing robots (Techrobots) mostly perform pick-and-place operations, that is, the robot grabs materials from the conveyor belt and places them on the pallet at the specified position along the motion path. Therefore, according to the positional relationship between the robot and the conveyor belt and the pallet when the robot completes the palletizing operation, comprehensively considering the obstacles in the movement process, the "door"-shaped movement track is selected. Note that when the robot end-effector completes the stacking of cartons at different positions on the pallet, the trajectory is all in the shape of a "door", and only the coordinates of the trajectory endpoint are different due to the different positions of the cartons on the pallet.
The so-called palletizing is based on the idea of integrated unitization, stacking materials according to a certain pattern into a stack, so that the unitized material stack can realize the storage, handling, loading and unloading, transportation, and other logistics activities of materials. Compared with traditional manual palletizing and gantry palletizers, palletizing robots have gradually been applied to various fields due to their high production efficiency, small footprint, large movement flexibility, and low labor intensity.
Commonly used palletizing robot hand grip
· Gripper type manipulator claw: mainly used for high-speed code bags;
· Splint type manipulator claw: mainly suitable for box stacking;
· Vacuum suction manipulator claw: mainly suitable for suckable stacking objects;
· Hybrid gripping manipulator claw: mainly suitable for picking up and stacking objects;
· Hybrid gripping manipulator claw: suitable for collaborative gripping and placing of several stations.
When using a palletizing robot, one important thing to consider is how the robot grasps a product. The vacuum gripper is the most common end-of-arm tool (EOAT). Relatively speaking, they are cheap, easy to operate, and can efficiently load most loads. However, in some specific applications, vacuum grippers may also encounter problems, such as porous substrates, flexible packaging with liquid content, or packaging with uneven surfaces.
Palletizing robot classification
1. According to the structure
According to the different mechanical structures, the palletizing robot includes the following three forms: Cartesian, rotary joint, and gantry crane.
① Cartesian palletizing robot: mainly composed of four parts: upright column, X-direction arm, Y-direction arm, and gripper, complete the palletizing of materials with four degrees of freedom (including three moving joints and one rotating joint). This type of palletizer has a simple structure, strong body rigidity, and large carrying weight, which is suitable for palletizing heavier materials.
② Rotary joint robot: The palletizer rotates around the body and includes four rotary joints: waist joint, shoulder joint, elbow joint, and wrist joint. This form of palletizer is programmed by teaching, that is, the operator holds the teaching box and controls the robot to move according to the prescribed action, so the moving process is stored in the memory, and this can be reproduced during automatic operation later. One exercise process. This kind of robot has a small body and a large range of motion. It can palletize one or several pallets at the same time, and can flexibly and flexibly work on a variety of product production lines.
③Gantry crane type: The robot arm is installed on the gantry crane as a gantry type palletizing robot. This type of palletizing robot has a large working range and can grasp heavier materials.
2. Divided according to stacking requirements
①Single layer palletizing robot
The single-layer palletizing robot is relatively basic. It mainly relies on the conveyor belt to transport materials. When it reaches the steering mechanism, it can be adjusted according to the specified direction. After preparation, it can enter the layer conveying mechanism. As long as the products are arranged tightly in this place according to the set arrangement order, the arranged products are transferred to the next station through the conveyor roller, so that the stacking operation of the palletizing robot is completed.
②Multilayer palletizing robot
There must be multiple layers corresponding to a single layer, which is definitely more complicated than a single layer palletizing robot. We can see whether the carrier board of the multi-layer palletizing robot is under the conveyor belt, or it can be left and right. When the machine is stacking, the materials will be neatly arranged on the pallet, and then the pallet will be set at the left limit position. When the materials conveyed by the conveyor belt are blocked by the baffle, they are arranged in a row. Then the pallet is moved to the right, and the materials will be lined up again like the steps above. By analogy, for each additional layer of material, the height of the lifting platform of the palletizing robot will drop by one layer until the material is stacked to a certain height and then stop.