Co-robots--open a new era of human-machine collaboration!
Date:2020-09-01
With the increase in labor costs and other factors, more and more robots enter the production field. How to make these robots directly and safely work side by side with employees has become the focus of research. This is how co-robots came into being.
1. Break down barriers, cooperate with man and machine, and work together
When asked how to imagine robots, most people think of large, bulky robots that work in the fences of large factories, or future armored warriors that imitate human behavior.
However, between the two, a new phenomenon has quietly emerged: the so-called "co-robot" appears, which can directly work with employees without having to use safety fences to isolate it.
This co-robot is expected to fill the gap between a fully manual assembly line and a fully automated production line. So far, some enterprises, especially small and medium-sized enterprises, still think that the cost of robot automation is too high and too complicated to consider the possibility of application.
Traditional industrial robots are generally huge and work behind glass shielding. It is widely used in the automotive industry and other large assembly lines.
In contrast, co-robots are lightweight, flexible, and easy to move, and can be reprogrammed to solve new tasks. This can help companies adjust to achieve more advanced small-batch processing to meet short-term production challenges.
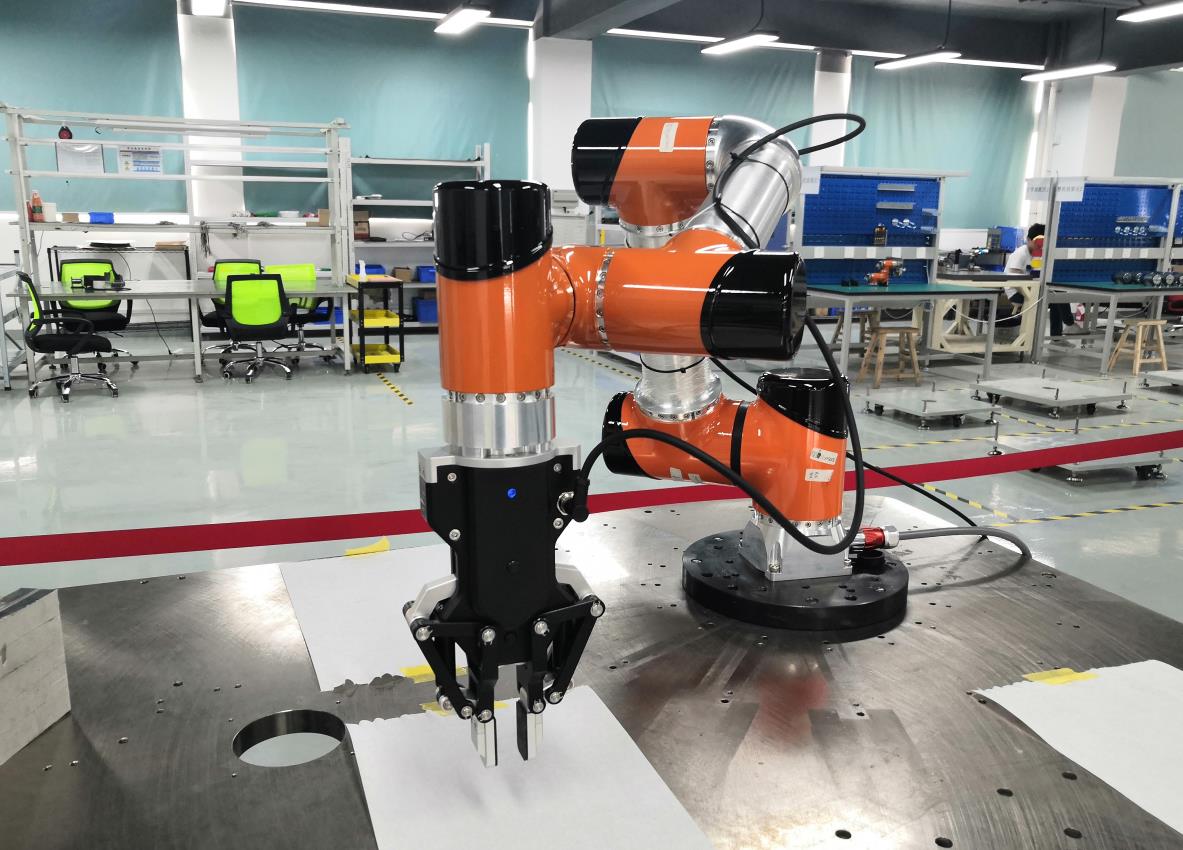
In the United States, the number of robots used in the automotive industry still accounts for about 65% of total market sales. The Robotics Industry Association of America (RIA) quoted observers' data as saying that so far, only 10% of companies that may benefit from robots have installed robots.
2. Plug and play robot
In terms of traditional robots, the capital cost of the robot itself only accounts for 25% to 30% of the total cost of the system. The remaining costs are related to robot programming, installation, and special shielding workshops.
The "out of the box" experience of a co-robot is usually less than an hour. This is the time required to uninstall, install, and write the first simple task program.
Why are co-robots user-friendly?
The robot does not rely on skilled programmers but is equipped with a flat touch screen user interface, and users can control the manipulator by displaying actions on the screen. Or, by easily holding the manipulator, show it the desired motion path. The interface complies with most industrial sensors and programmable logic controller (PLC) standards.
Many low-cost, easy-to-use robotic tools can be quickly applied to most companies' manufacturing processes, which is why it is not difficult to imagine the explosive growth of co-robots in the past two years.
1. Break down barriers, cooperate with man and machine, and work together
When asked how to imagine robots, most people think of large, bulky robots that work in the fences of large factories, or future armored warriors that imitate human behavior.
However, between the two, a new phenomenon has quietly emerged: the so-called "co-robot" appears, which can directly work with employees without having to use safety fences to isolate it.
This co-robot is expected to fill the gap between a fully manual assembly line and a fully automated production line. So far, some enterprises, especially small and medium-sized enterprises, still think that the cost of robot automation is too high and too complicated to consider the possibility of application.
Traditional industrial robots are generally huge and work behind glass shielding. It is widely used in the automotive industry and other large assembly lines.
In contrast, co-robots are lightweight, flexible, and easy to move, and can be reprogrammed to solve new tasks. This can help companies adjust to achieve more advanced small-batch processing to meet short-term production challenges.
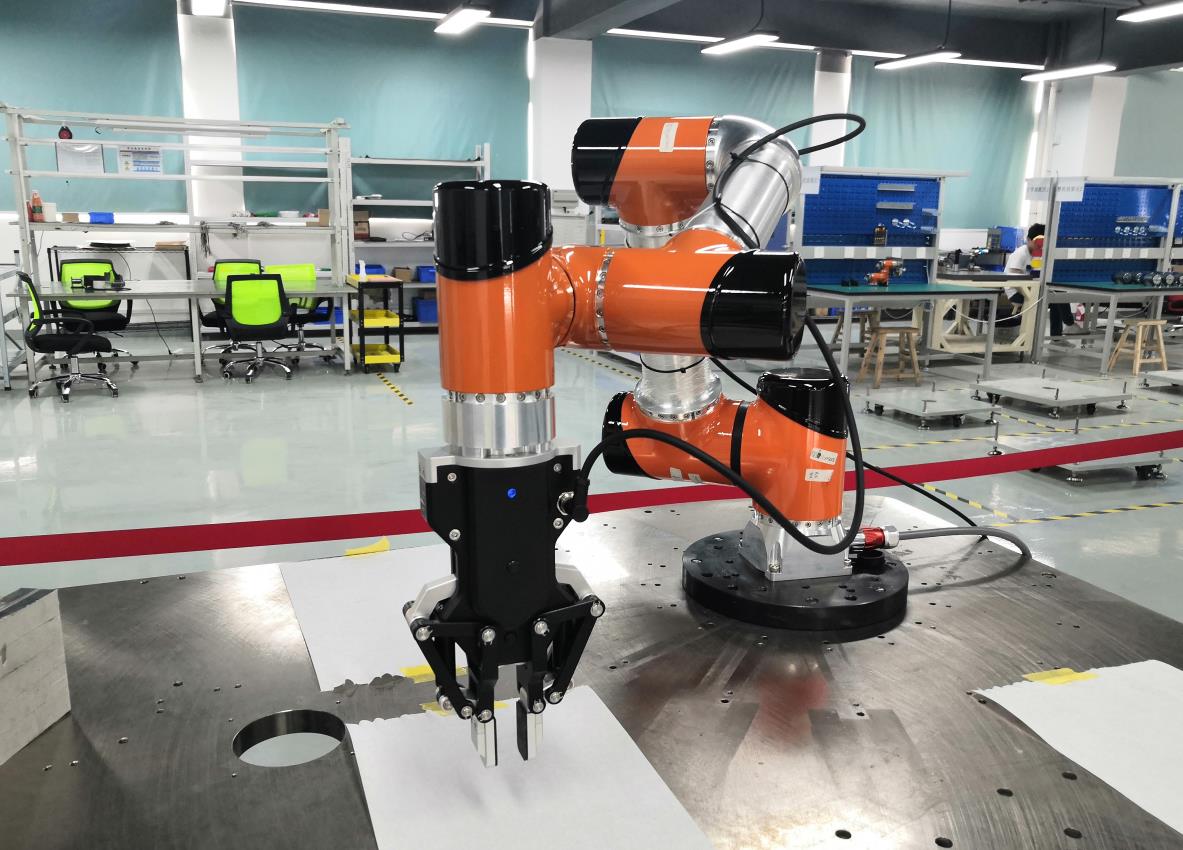
In the United States, the number of robots used in the automotive industry still accounts for about 65% of total market sales. The Robotics Industry Association of America (RIA) quoted observers' data as saying that so far, only 10% of companies that may benefit from robots have installed robots.
2. Plug and play robot
In terms of traditional robots, the capital cost of the robot itself only accounts for 25% to 30% of the total cost of the system. The remaining costs are related to robot programming, installation, and special shielding workshops.
The "out of the box" experience of a co-robot is usually less than an hour. This is the time required to uninstall, install, and write the first simple task program.
Why are co-robots user-friendly?
The robot does not rely on skilled programmers but is equipped with a flat touch screen user interface, and users can control the manipulator by displaying actions on the screen. Or, by easily holding the manipulator, show it the desired motion path. The interface complies with most industrial sensors and programmable logic controller (PLC) standards.
Many low-cost, easy-to-use robotic tools can be quickly applied to most companies' manufacturing processes, which is why it is not difficult to imagine the explosive growth of co-robots in the past two years.
Previous Article: The difference between co-robots and traditional six-axis industrial robots
Next Article: Techrobots explore more applicable fields of co-robots