There is a long way to go to conquer the three core technologies and markets of industrial robots
Date:2019-06-13Industrial robots refer to multi-joint manipulators or multi-degree-of-freedom machine equipment for industrial field. Man's actions are controlled by the brain, which sends out instructions to drive muscles and bones to respond through the assistance of cerebellum and nerves. The same is true for robots. The controllers of the control systems in the three systems play the role of the brain. The servo and the reducer in the power system play the role of driving. They receive the control system instructions and transmit them to the mechanical system which is isomorphic with muscles and bones. The mechanical system is composed of fuselage, arm and other components. It is loaded and practical. Complete the exercise. To sum up, the robot industry chain is mainly composed of the upstream R&D manufacturers of core components such as controllers, servers and reducers, the upstream R&D manufacturers of robot ontology composed of mechanical components, and the downstream system integrators involved in vertical solutions of the industry. The scale ratio of the upper, middle and lower markets is about 2:3:10, and the local competitiveness is low, medium and high respectively. Gross interest rates are 30%-40%, 10%-20% and 30%-40% respectively. With its large scale, strong local competitiveness and high gross interest rate, the downstream market has become an indispensable place.
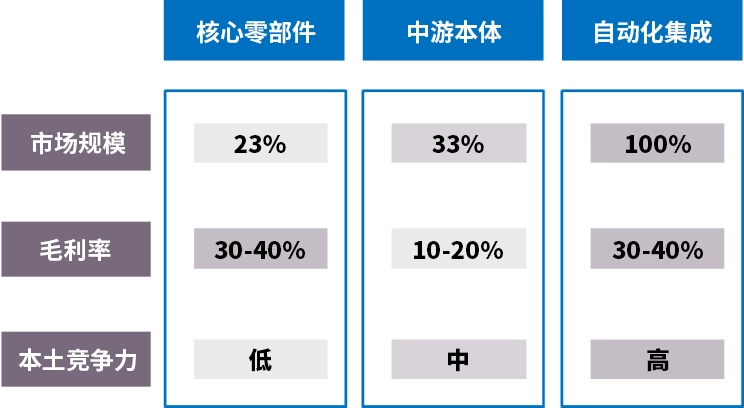
The downstream integration solution provider mainly refers to the further development of software and the customization of system integration for customers. According to the working nature and scene, it can be divided into handling (loading and unloading, palletizing), processing (drilling, welding, spray painting, laser cutting, polishing, painting), inspection, assembly (assembly, packaging) and so on. It is mainly used in automobile, electronics, metal processing and other subdivision industries. At present, due to the lack of technical barriers and the inadequate depth of service for international brands, most domestic enterprises gather here. In 2017, there were more than 3000 industrial robot system integrators, and the domestic coverage rate was more than 90%. The leader harvests the market and eliminates the small players with the advantages of strong resource integration ability, professional and profound industry understanding, and enough funds to cope with the "3331" payment cycle, which makes the competition white-hot.
The main mechanical parts of the middle reaches are the frame (part has walking structure), fuselage, arm, wrist, hand and so on. The overall trend is intelligent, lightweight and movable. According to the mechanical structure, it can be divided into rectangular coordinate type, cylindrical coordinate type, spherical coordinate type and joint coordinate type. Cartesian coordinate type moves around X, Y and Z axes, which is suitable for material handling in large workspace; cylindrical coordinate type can be used for lifting, rotating and telescoping; spherical coordinate type can be used for rotating, pitching and telescoping; joint coordinate type has many rotating joints, and the following are the mainstream: vertical multi-joint type, of which six axes include rotating S. Each axis is driven by servo motor and axle reducer, which is widely used in automotive and electronic production processes. Planar multi-joint SCARA is suitable for small-scale and high-speed motion, such as precision assembly in 3C industry; Parallel joint Delta, which is connected in series. Type B has higher precision, greater degree of freedom and strong bearing capacity. It is mainly used for high-speed fetching and placing and screening. Automatic guided transport AGV is mainly used in intelligent warehousing.
At present, the main body is "four families". In 2017, sales of Fanaco, Kuka, ABB and Ankawa accounted for 49.3% of the world's total, while domestic industrial robot brands accounted for only 25% of the Chinese market. Due to the lack of control over the upstream and downstream of the industrial chain, barriers can not be formed and markets can not be obtained. Moreover, this part of the international competition is strong, and gross interest rate is relatively low. Unless companies with strong technology and resource integration capabilities, domestic manufacturers seldom enter this module alone at present.
Upstream reducer, server and controller are the three core components of industrial robots, accounting for nearly 70% of the total cost. Among them, reducer accounts for up to 40% and technical barriers are the strongest, which directly affects the speed and accuracy of robots. Therefore, breakthroughs in this technology can give enterprises higher bargaining power. At present, the two main types of reducers, RV and harmonic, Japanese manufacturers Nabotsk and Hammenako occupy 60% and 15% of the market respectively. Due to technology and precision manufacturing capability, the localization rate of core components is the lowest in the whole industry chain. The localized substitution of industrial robots needs to penetrate the underlying core components in order to ensure the smooth realization of localized substitution in the international environment such as Sino-US trade frictions. Therefore, to conquer this part of technology and market is a long way to go and imperative for Chinese enterprises.