How to choose a suitable co-robot in a research project?
Date:2020-08-24In the past few years, co-robots have been one of the most compelling success stories in robotics and automation.
Due to its inherent quality and ease of integration, co-robots have been adopted by global business and research projects.
Your research project may be narrow at the moment, but it may be more demanding, or you may want to use co-robots in different research projects. Versatility is a key attribute of co-robots. It provides researchers with the possibility of using co-robots in different projects, and even sharing co-robots between different research teams.
Many new and existing robot manufacturers are providing co-robots that can be used in research projects. Researchers can now choose the most suitable co-robot for their project instead of using existing co-robots on the market.
The following are some of the key options and features you should pay attention to when choosing a co-robot:
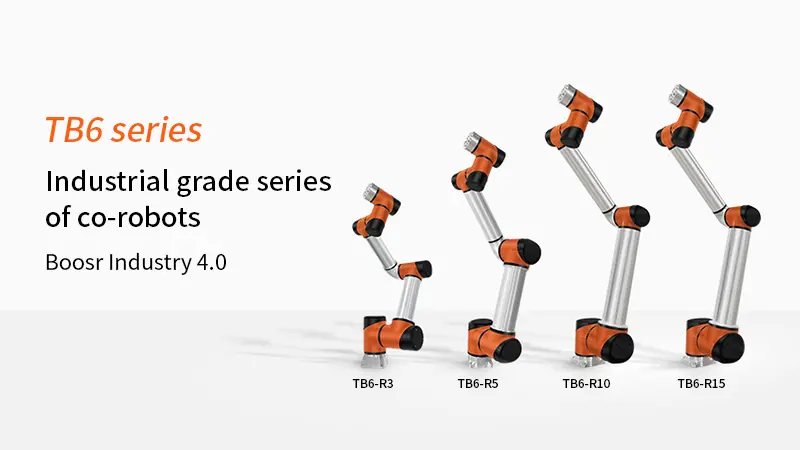
Degree of freedom:
The number of minor axes is also called degrees of freedom. The degree of freedom refers to the number of independent displacements or movements that a co-robot can perform. Most co-robots have 6 or 7 degrees of freedom. For example, a person’s arm has 7 degrees of freedom, so if your project involves imitating or understanding the movement of a person’s arm, you need to choose a co-robot with 7 degrees of freedom. If your project involves selection, classification, etc., in most cases, a six-degree-of-freedom co-robot is sufficient, unless there is a complex co-robot.
Payload and reach:
It's very simple. The payload capacity of most co-robots ranges from 3 kg to 20 kg. However, you need to know more about whether it includes the necessary end of the arm tool, and how heavy is the gripper you want to use? Is the payload calculated within the maximum reach of the arm? When determining the maximum payload capacity, it is best to leave some room for future payloads. The same is true for the total coverage of co-robots. Note that the movement of the co-robot may be most restricted.
Communication rate:
This will play a role in some typical research projects. For example, if you are engaged in human-computer interaction (HRI) or any other project that requires near-instant communication, you may need to check the communication rate of the co-robot. Some co-robots offer a frequency of 1 KHZ as an option, which means a response time of 1ms. This is ideal for near-instant communication.
Force/torque induction:
Some co-robots have built-in force/torque sensing in each joint. All co-robots provide external force/torque sensing. If your research requires force feedback, it is useful to install sensors on each joint. Only when the arm touches the object through the sensor, the external sensor of the arm can provide feedback. If the elbow or other part of the co-robot touches anything, it will not provide feedback.
Collaborative security:
Most co-robots have similar safety standards. Depending on your project and how the co-robot interacts with people, you should look at safety mechanisms and options, such as safety stop buttons, backward functions, and so on. If you want to use co-robots for collaborative and non-cooperative projects, it is best to choose to provide co-robots with the option to turn off the collaborative model.
If the co-robot wants to work close to humans, you may need to check the external stop option after activating the switch and the stop time of the co-robot.
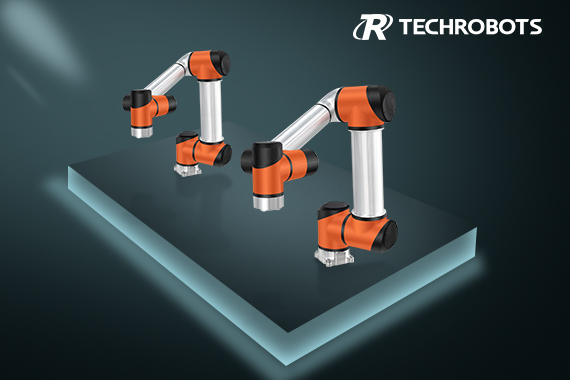
Mobility:
Most co-robots can be easily integrated with mobile platforms. If you want to seamlessly integrate with mobile platforms, you can look for OEM options provided by some co-robot manufacturers. In this way, the control cabinet can be peeled off, and the electrical equipment of the co-robot can be installed on the main body of the mobile platform. This option does not apply to all co-robots.