Human-machine collaboration technology, where is the development direction of flexible robot
Date:2020-05-14
After decades of development, industrial robots have been used in different production and manufacturing processes, but there are still many production processes that need to be completed manually. Robot workers make up less than 1% of the workforce, and demand for them is far from being met. This demand would be greater if the scope were extended to more productive activities, such as commerce, medical rehabilitation, and so on. In the face of these demands, can robots solve these problems? What kind of robot do we need?
Advantages and disadvantages of industrial robots
Traditional industrial robots are developed based on servo motors. Compared with artificial robots, traditional industrial robots have the advantages of large carrying capacity, fast speed and high positioning accuracy. Its disadvantage is: intelligence degree is low, deploy in different environment inconvenient, time-consuming and laborious. On the basis of traditional industrial robot, co-robot realizes the safety guarantee of working in the same space with human by reducing the structural weight and limiting the power and speed of the motor. Essentially, co-robot is a branch of industrial robot.
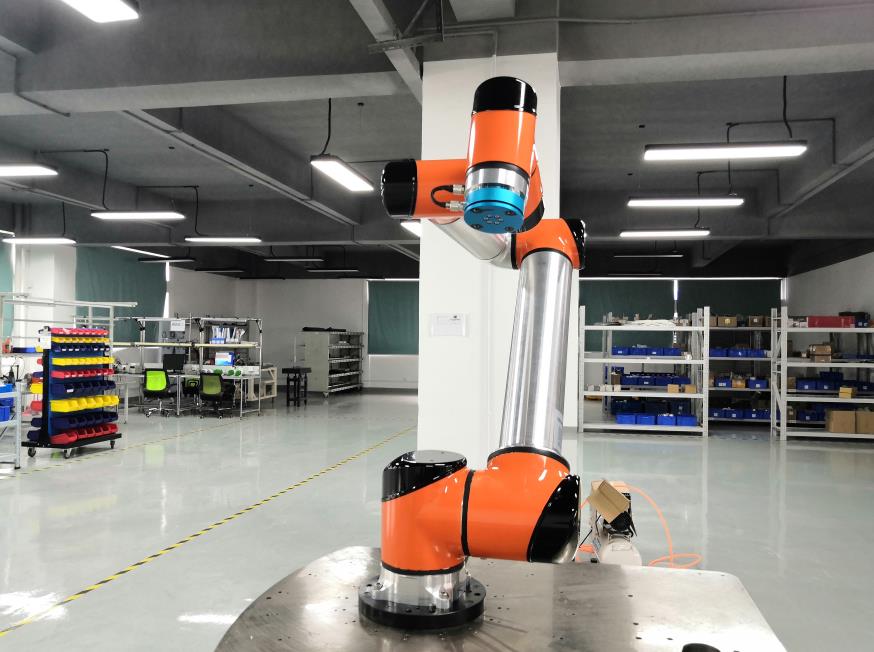
The control position of industrial robots generally adopts the drag-and-teach function. This method can only be applied to strictly structured scenes and cannot deal with the uncertainties in the scenes well. For example, the assembly precision of the parts is much higher than the position control precision of the robot, and the assembly cannot be completed by the position control alone. The flexibility of hand power and arm, as well as the ability to learn and make decisions, can easily complete the assembly movement. Therefore, currently, factories need a large number of workers to assemble parts, and industrial robots have made a lot of application attempts in this field, but it is difficult to compete for manpower effectively.
If the application of robots extends to commercial, medical rehabilitation and other broad production activities, such as rehabilitation physiotherapy, industrial robots are completely vulnerable to human arm injury in these scenarios. Doctors rely more on arm strength to help patients complete nursing movements, while traditional industrial robots are difficult to achieve compliance with human arm muscle control. At present, traditional industrial robots still have a large number of artificial replacement inventory scenarios, but for industrial assembly, production activities in a broad sense, the ability to truly compete for the human arm is the goal of the next stage of the robotic arm.
What's the difference between a flexible robot? What are the benefits?
Although traditional industrial robots can also realize force sense control through terminal force sensors, due to the limitation of position-oriented control structure, there are many closed-loop links of force sense, with slow response and slow beat frequency, which are difficult to compare with human hands. The flexible robot is different from the traditional industrial robot in hardware and software structure: each joint is equipped with powerful sensors, and the underlying control structure changes from the original position control to the position fusion control, so that the robot has high precision position control and high dynamic force control.
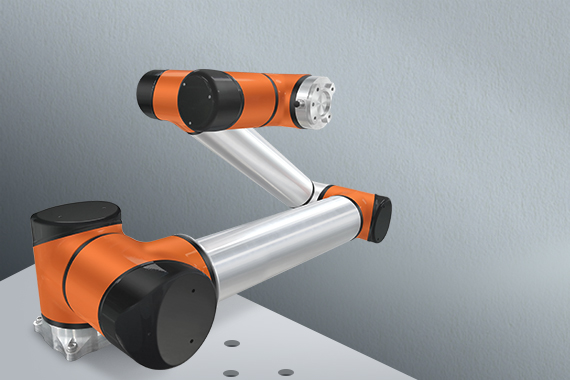
The so-called high dynamic force control means that the closed-loop frequency of the force is two orders of magnitude higher than that of the industrial robot, and the force sense response is more sensitive. At the same time, it can simulate the flexibility of human arm muscle control, so that the robot has the ability to deal with environmental uncertainty. For example, in the component assembly scene, the active compliance in the corresponding direction can be controlled to simulate the position deviation of human hands for the flexible assembly. For example, in the case of complex surface grinding, the position of the flexible robot is controlled in the forward direction, and the force is controlled in the direction of grinding pressure. Through the flexible adjustment of the mechanical arm, the robot ADAPTS to the bending of the surface, which is consistent with the characteristics of manual operation.
Relying on the high dynamic force control technology, the characteristics of the current co-robot can be comprehensively improved: for example, through the sensitive force perception, the robot can be more portable drag teaching, or even directly drag the robot to write calligraphy, making the robot easier to use. Through the high sensitivity of external collision detection, man-machine cooperation is more secure.
If artificial intelligence is compared with human decision making, the motion control of the robot's arm is similar to that of the cerebellum and limbs, except that the limbs controlled by position are not coordinated. The addition of force sense and flexibility provides a stronger platform support for the upper intelligence, which can accelerate the landing of artificial intelligence in the generalized production activities.
Through the above core technical features, flexible robots can solve the application shortcomings of traditional industrial robots in production and assembly, and can be extended to a wider range of scenarios such as auxiliary medical care and commercial services.
Advantages and disadvantages of industrial robots
Traditional industrial robots are developed based on servo motors. Compared with artificial robots, traditional industrial robots have the advantages of large carrying capacity, fast speed and high positioning accuracy. Its disadvantage is: intelligence degree is low, deploy in different environment inconvenient, time-consuming and laborious. On the basis of traditional industrial robot, co-robot realizes the safety guarantee of working in the same space with human by reducing the structural weight and limiting the power and speed of the motor. Essentially, co-robot is a branch of industrial robot.
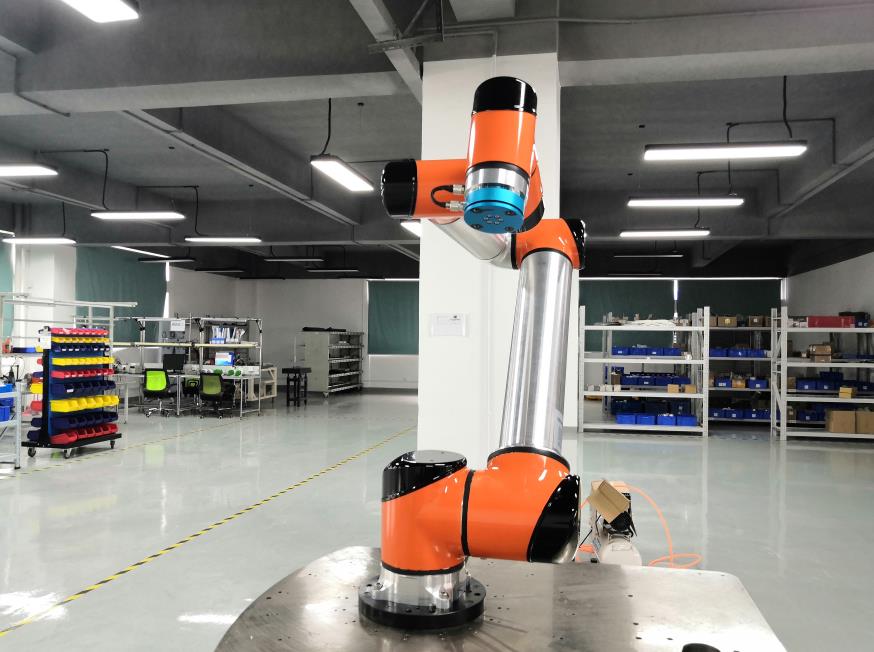
The control position of industrial robots generally adopts the drag-and-teach function. This method can only be applied to strictly structured scenes and cannot deal with the uncertainties in the scenes well. For example, the assembly precision of the parts is much higher than the position control precision of the robot, and the assembly cannot be completed by the position control alone. The flexibility of hand power and arm, as well as the ability to learn and make decisions, can easily complete the assembly movement. Therefore, currently, factories need a large number of workers to assemble parts, and industrial robots have made a lot of application attempts in this field, but it is difficult to compete for manpower effectively.
If the application of robots extends to commercial, medical rehabilitation and other broad production activities, such as rehabilitation physiotherapy, industrial robots are completely vulnerable to human arm injury in these scenarios. Doctors rely more on arm strength to help patients complete nursing movements, while traditional industrial robots are difficult to achieve compliance with human arm muscle control. At present, traditional industrial robots still have a large number of artificial replacement inventory scenarios, but for industrial assembly, production activities in a broad sense, the ability to truly compete for the human arm is the goal of the next stage of the robotic arm.
What's the difference between a flexible robot? What are the benefits?
Although traditional industrial robots can also realize force sense control through terminal force sensors, due to the limitation of position-oriented control structure, there are many closed-loop links of force sense, with slow response and slow beat frequency, which are difficult to compare with human hands. The flexible robot is different from the traditional industrial robot in hardware and software structure: each joint is equipped with powerful sensors, and the underlying control structure changes from the original position control to the position fusion control, so that the robot has high precision position control and high dynamic force control.
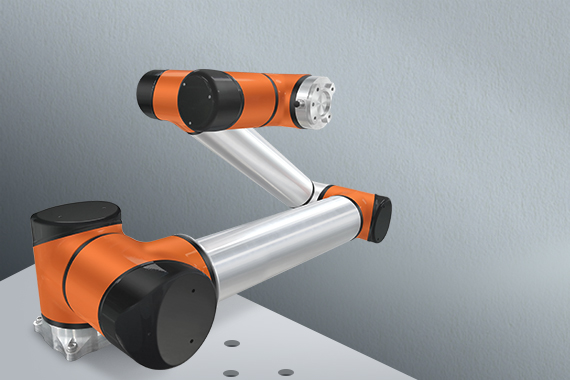
The so-called high dynamic force control means that the closed-loop frequency of the force is two orders of magnitude higher than that of the industrial robot, and the force sense response is more sensitive. At the same time, it can simulate the flexibility of human arm muscle control, so that the robot has the ability to deal with environmental uncertainty. For example, in the component assembly scene, the active compliance in the corresponding direction can be controlled to simulate the position deviation of human hands for the flexible assembly. For example, in the case of complex surface grinding, the position of the flexible robot is controlled in the forward direction, and the force is controlled in the direction of grinding pressure. Through the flexible adjustment of the mechanical arm, the robot ADAPTS to the bending of the surface, which is consistent with the characteristics of manual operation.
Relying on the high dynamic force control technology, the characteristics of the current co-robot can be comprehensively improved: for example, through the sensitive force perception, the robot can be more portable drag teaching, or even directly drag the robot to write calligraphy, making the robot easier to use. Through the high sensitivity of external collision detection, man-machine cooperation is more secure.
If artificial intelligence is compared with human decision making, the motion control of the robot's arm is similar to that of the cerebellum and limbs, except that the limbs controlled by position are not coordinated. The addition of force sense and flexibility provides a stronger platform support for the upper intelligence, which can accelerate the landing of artificial intelligence in the generalized production activities.
Through the above core technical features, flexible robots can solve the application shortcomings of traditional industrial robots in production and assembly, and can be extended to a wider range of scenarios such as auxiliary medical care and commercial services.