Choose the right encoder for the robot
Date:2020-01-09
In the development process of industrial robots, the focus of car manufacturing and application began to shift to industrial application, and the application scale became more extensive with the speed, stability, safety, accuracy, control and availability. Therefore, the selection and application of precise positioning control has been paid more and more attention to.
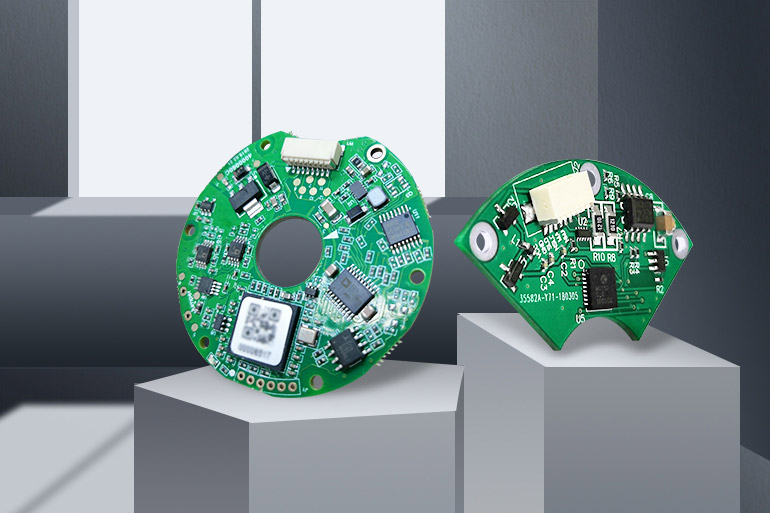
Car industry is the most mature industry of application robots, accounting for nearly 40% of the total market share. When the repetitive accuracy of the robot reaches ± 0.02mm, it can meet the accuracy requirements of the car manufacturing industry. Most of the car industrial robots will be equipped with sealed rotary absolute optical encoder, while other robots will use magnetic and inductive encoder or ring angle resolver.
However, the application of industrial robots will gradually shift from focusing on car manufacturing to other industries. Robot application in the electronic industry (also known as 3C industry) accounts for about 30% of the market share. With the electronic products becoming more and more delicate and light, the parts are more and more refined, and the requirements for the accuracy of robot motion control are higher and higher.
select encoder to ensure robot precision
No matter how well designed the robot itself is, it still needs to rely on the components used to give full play to its function and utility. Robot is usually composed of main body, servo drive system, reducer and control system. The manipulator needs to accept the joints of the robot so that the orientation can be fed back at any time. Therefore, the encoder is also an indispensable component to ensure the accuracy of the robot.
In general, two types of encoders are used when planning robots: optical and magnetic.
The difference between magnetic encoder and optical encoder in the principle of azimuth sensing will result in different efficiency results due to different environmental conditions. The magnetic encoder adopts Hall sensor technology, which can output reliable digital signal feedback in severe environmental conditions. It has the characteristics of wide operating temperature, high impact resistance and anti-seismic ability, stable sealing and anti pollution, and its non touch delicate and light planning can ensure the long-term and stable operation.
Optical encoder uses optics to identify encoder position, which is superior to magnetic encoder in resolution or precision. When choosing the right encoder for robot planning, we must judge it according to the efficiency we pay attention to: is it a high precision optical encoder or a magnetic encoder which is still reliable under the condition of pole environment?
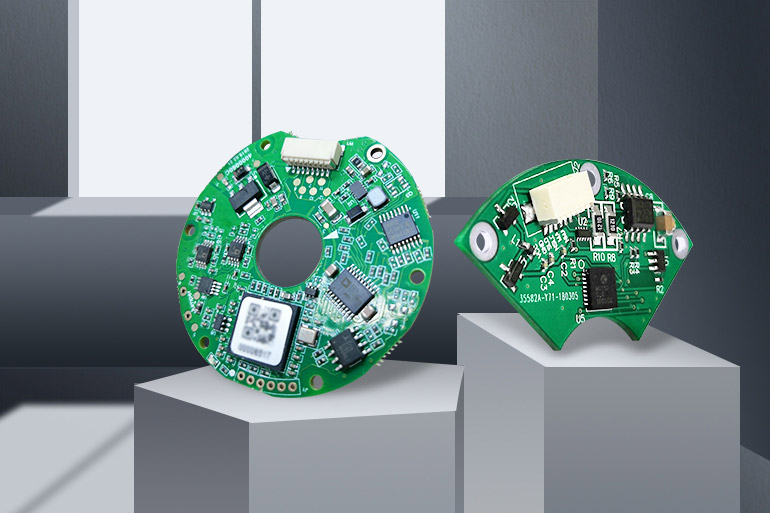
Car industry is the most mature industry of application robots, accounting for nearly 40% of the total market share. When the repetitive accuracy of the robot reaches ± 0.02mm, it can meet the accuracy requirements of the car manufacturing industry. Most of the car industrial robots will be equipped with sealed rotary absolute optical encoder, while other robots will use magnetic and inductive encoder or ring angle resolver.
However, the application of industrial robots will gradually shift from focusing on car manufacturing to other industries. Robot application in the electronic industry (also known as 3C industry) accounts for about 30% of the market share. With the electronic products becoming more and more delicate and light, the parts are more and more refined, and the requirements for the accuracy of robot motion control are higher and higher.
select encoder to ensure robot precision
No matter how well designed the robot itself is, it still needs to rely on the components used to give full play to its function and utility. Robot is usually composed of main body, servo drive system, reducer and control system. The manipulator needs to accept the joints of the robot so that the orientation can be fed back at any time. Therefore, the encoder is also an indispensable component to ensure the accuracy of the robot.
In general, two types of encoders are used when planning robots: optical and magnetic.
The difference between magnetic encoder and optical encoder in the principle of azimuth sensing will result in different efficiency results due to different environmental conditions. The magnetic encoder adopts Hall sensor technology, which can output reliable digital signal feedback in severe environmental conditions. It has the characteristics of wide operating temperature, high impact resistance and anti-seismic ability, stable sealing and anti pollution, and its non touch delicate and light planning can ensure the long-term and stable operation.
Optical encoder uses optics to identify encoder position, which is superior to magnetic encoder in resolution or precision. When choosing the right encoder for robot planning, we must judge it according to the efficiency we pay attention to: is it a high precision optical encoder or a magnetic encoder which is still reliable under the condition of pole environment?