Four Common Control Modes of Industrial Robots
Date:2019-08-05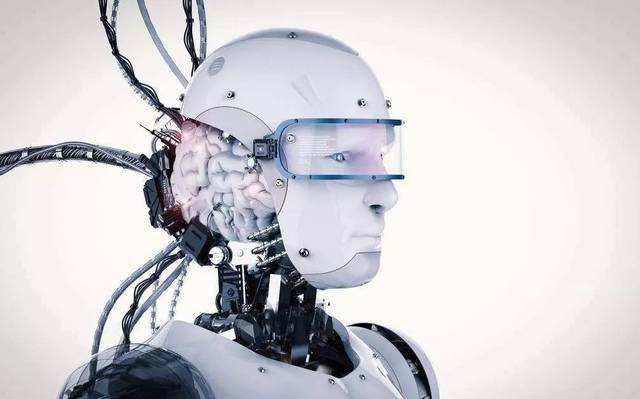
1. Point position control mode
This control method only controls the position and posture of the end effector of industrial robot at some specified discrete points in the working space. In control, only industrial robots are required to move quickly and accurately between adjacent points, and there are no rules for the trajectory of the target point. The positioning accuracy and the time required for motion are the two main technical indicators of this control mode. This control method has the characteristics of easy realization and low positioning accuracy. Therefore, it is often used in loading and unloading, handling, spot welding and inserting components on the circuit board, which only require the accurate position and posture of the end effector at the target point. This method is relatively simple, but it is very difficult to achieve the positioning accuracy of 2-3um.
2. Continuous trajectory control
This control method is to control the position and posture of the end effector of industrial robot continuously in the working space. It requires that the end effector of industrial robot move in a certain precision range strictly according to the predetermined trajectory and speed, and that the speed is controllable, the trajectory is smooth and the motion is smooth, so as to complete the task. The joint of the industrial robot moves continuously and synchronously, and the end effector of the robot can form a continuous trajectory. The main technical index of this control method is the trajectory tracking accuracy and stability of the industrial robot's end effector posture. Usually, arc welding, painting, deburring and inspection robots adopt this control method.
3. Torque Control Mode
In the process of assembling and grasping objects, besides accurate positioning, the force or moment used must be appropriate. At this time, servo mode must be used. The principle of this control mode is basically the same as that of position servo control, except that input and feedback are not position signals, but force (moment) signals, so powerful (moment) sensors must be used in the system. Sometimes adaptive control is also implemented by using the sensing functions such as proximity and sliding.
4. Intelligent Control Mode
Intelligent control of robots is to acquire knowledge of the surrounding environment through sensors, and make corresponding decisions according to their own internal knowledge base. By using intelligent control technology, the robot has strong environmental adaptability and self-learning ability. The development of intelligent control technology depends on the rapid development of artificial intelligence such as artificial neural network, genetic algorithm, genetic algorithm and expert system in recent years. Perhaps this mode of control, industrial robots are really a bit of "artificial intelligence" landing taste, but also the most difficult to control well, in addition to the algorithm, but also depends heavily on the accuracy of components.
From the point of view of control essence, industrial robots are still in the lower level of space positioning control in most cases. They do not have much intelligence. They can be said to be only a relatively flexible manipulator, which is still a long way from "human".
Previous Article: How long will it take for China to make robots?
Next Article: Five Trends of Industrial Robots in the Future