Seven working scenarios of co-robots
Date:2020-11-12In the past few years, co-robots have led to the rapid growth of the robotics market. According to data, by 2021, the market sales of co-robots will reach 150,000 units, and the sales amount is expected to increase to US$2 billion. Many industries have begun to introduce co-robots to find a new way to develop automation.
Co-robots stand out because they can play an important role in the field of work that was initially done manually. Due to the inherent safety of co-robots, such as the use of force feedback and collision detection, the safety of human and co-robot work will be guaranteed. Techrobots one of the domestic co-robot manufacturers, recently listed seven common work areas for co-robots.
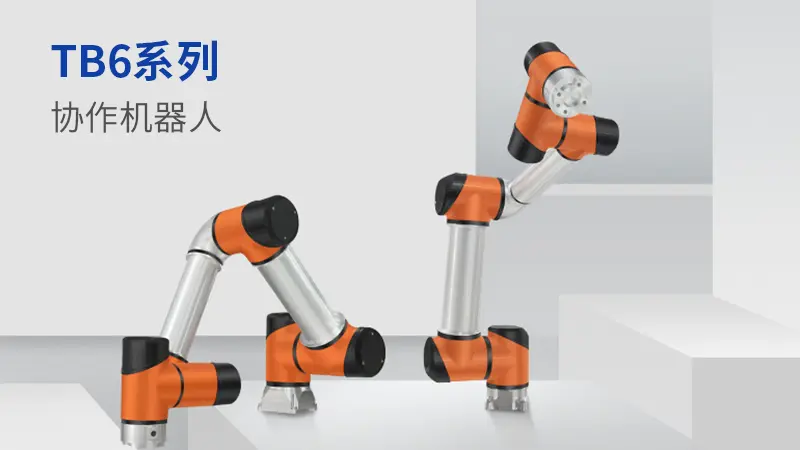
Grab and place
A typical grab and place robot. The robot can recognize parts and objects and pack them.
For workers, manual picking and placing should be one of the most repetitive tasks every day. Boring operations can easily lead to worker errors, and highly repetitive body movements can easily lead to physical fatigue and injury. The use of co-robots from grasping and placing tasks is a good start to reduce repetitive workers. Picking and placing tasks refer to picking and placing workpieces in another location. In actual production, this operation can be used to pick up items from pallets or conveyor belts for packaging or sorting. Grabbing from the conveyor belt also requires advanced vision system support. A picking co-robot needs an end effector to grab an object. This object can be a fixed device, a vacuum suction device, or a gripper.
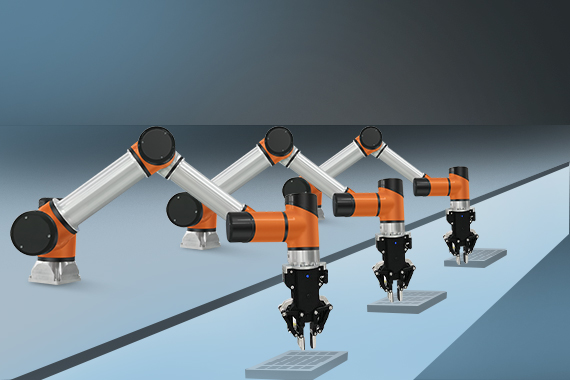
Equipment care
Equipment care requires workers to stand in front of CNC machine tools, injection molding machines, or other similar equipment for a long time to pay attention to the operating needs of the machine, such as changing tools or supplementing raw materials. This process is very time-consuming for operators. In this case, the use of co-robots can not only liberate employees but also allow co-robots to maintain multiple machines and increase productivity. The nursing co-robot needs to equip specific equipment with I/O docking hardware. This hardware prompts when the robot enters the next production cycle or needs to replenish raw materials.
Packing pallet
Product packaging and pallets belong to a subcategory of the pick and place category. Before leaving the factory floor, the product needs to be properly prepared for transportation, including shrink packaging, box assembly and loading, box organization, and pallets ready for shipment. This kind of work repetition rate is high, the load is small, and it is very suitable for replacing manual work with co-robots. Rapid product upgrading is the key to the operation of production enterprises. This application requires the use of conveyor tracking to synchronize the movement of the robot and the conveyor. For products with inconsistent shapes, the application also needs to be integrated with the vision system.
Processing operation
Machining is any process that requires the use of tools to manipulate the workpiece. In the welding process, distribution, and welding process, co-robots are often used. Each of these processing tasks requires the use of tools to repeat a fixed path. If new employees use these tasks, a lot of time is needed for training to meet the requirements of the finished product. With co-robots, you can copy them to other robots by programming on one robot. At the same time, the co-robot also solves the accuracy and repeatability of workers. Traditional welding robot systems usually require operators to have very professional robot programming and welding knowledge.
The advantage of the co-robot system is realized through positioning, position recording, or traditional CAD/CAM programming, which simplifies the robot programming process and enables workers with only welding experience to complete the programming of the co-robot.
Precision Machining
Hand tools must be used for manual finishing operations, and the processing process is usually very laborious. The vibration caused by the tool may also cause injury to the operator. Co-robots can provide the strength, repeatability, and accuracy required to complete the process. The types of finishing performed by the robot include polishing, grinding, and deburring. The robot can complete the corresponding operation through manual teaching or computer programming. The force control system of the co-robot makes the robot more durable. Through the end effector or the built-in force-sensing device, precision machining of parts of different sizes can be realized.
Quality inspection
The co-robot can also check the quality of the parts. This process usually includes a comprehensive inspection of finished products, high-resolution image inspection of precision parts, and comparison and confirmation of parts and CAD models. Fixed multiple high-resolution cameras can automate the quality inspection process of co-robots and obtain inspection results quickly. The use of co-robots for inspection can obtain high-quality inspections and can obtain more accurate production batches. The completion of the inspection requires the installation of an end driver, vision system, and software with a high-resolution camera.
Previous Article: Micro-robots usher in new opportunities in 2019
Next Article: How do humans and robots cooperate in the era of artificial intelligence?