Collaborative robots with integrated vision recognition systems for intelligent stacking
Date:2023-03-20
Machine vision systems can replace human eyes in tasks such as measurement, positioning, identification, and detection. They overcome issues like inconsistency, non-repeatability, and subjectivity associated with human standards. By establishing digital standards for quality control, these systems surpass human limits in speed, hyperspectral analysis, high resolution, reliability, and exhibit continuous operation and environmental adaptability. Collaborative robots, coupled with machine vision, have made significant breakthroughs and find widespread applications in industries such as automated manufacturing, retail, logistics, e-commerce, pharmaceuticals, and food.
With the rapid development of domestic smart manufacturing, logistics, and e-commerce industries, sorting and stacking operations face high intensity and repetitive tasks, resulting in low quality and efficiency in manual operations. Automated sorting and stacking systems have emerged to address this challenge. In traditional automated stacking operations, the arrangement of incoming materials is often disorderly and random. Using traditional manual teaching methods is difficult and inefficient, limiting the scope of automation. To address this issue, Tech Robots has developed a smart stacking solution equipped with a vision recognition system for collaborative robots. This system can achieve sorting and stacking of unordered items, ensuring stable stacking patterns and optimal use of space. The entire process is fully automated, requiring no manual intervention.
Using industrial-grade cameras with high precision, large field of view, and extended depth of field, specifically designed for disassembly and stacking scenarios. The camera captures image information, transmitting it to the robot control platform software. The platform software incorporates built-in vision algorithms and intelligent trajectory planning algorithms. Incoming boxes can be placed randomly, and the visual algorithm quickly and accurately identifies the position of the boxes. The intelligent trajectory planning algorithm provides precise gripping points, placement points, and trajectory points, guiding the collaborative robot in rapid picking and stacking actions, placing items in specified locations.
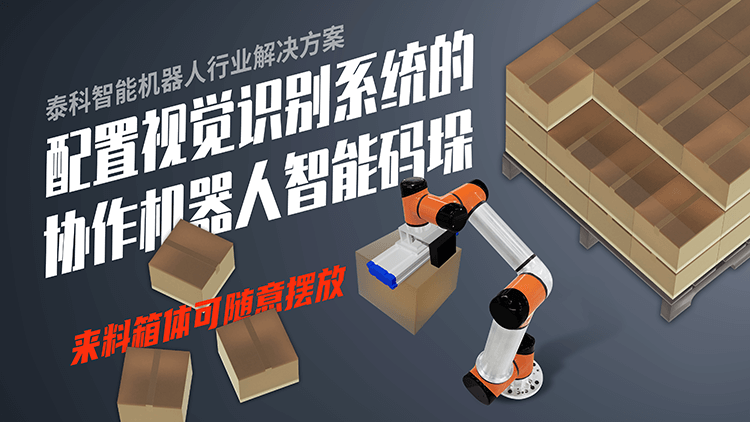
This solution utilizes the Tech Robots TB6 series collaborative robot equipped with a vision recognition system and end-of-arm tooling. The positioning accuracy can reach ±0.03mm, accommodating different loads ranging from 3 to 20KG (customizable for a larger 30KG load). The robot features collision detection, ensuring safe and reliable human-robot collaboration. It offers stable performance, simplicity, flexibility in angle installation, quick deployment, space-saving, and a one-stop OEM customization service.
The overall solution demonstrates high intelligence, with characteristics such as high precision, strong resistance to ambient light, and the ability to handle dark-colored objects. It accurately applies to various items like boxes, packaging boxes, material boxes, woven bags, and workpieces. It can handle complex situations like labels, straps, tapes, patterns, reflective films, and is unaffected by the pose of the placed objects. The robot incorporates advanced algorithms for trajectory planning and can be configured to grasp single or multiple objects in a single operation, effortlessly handling various box sizes and common stacking patterns.